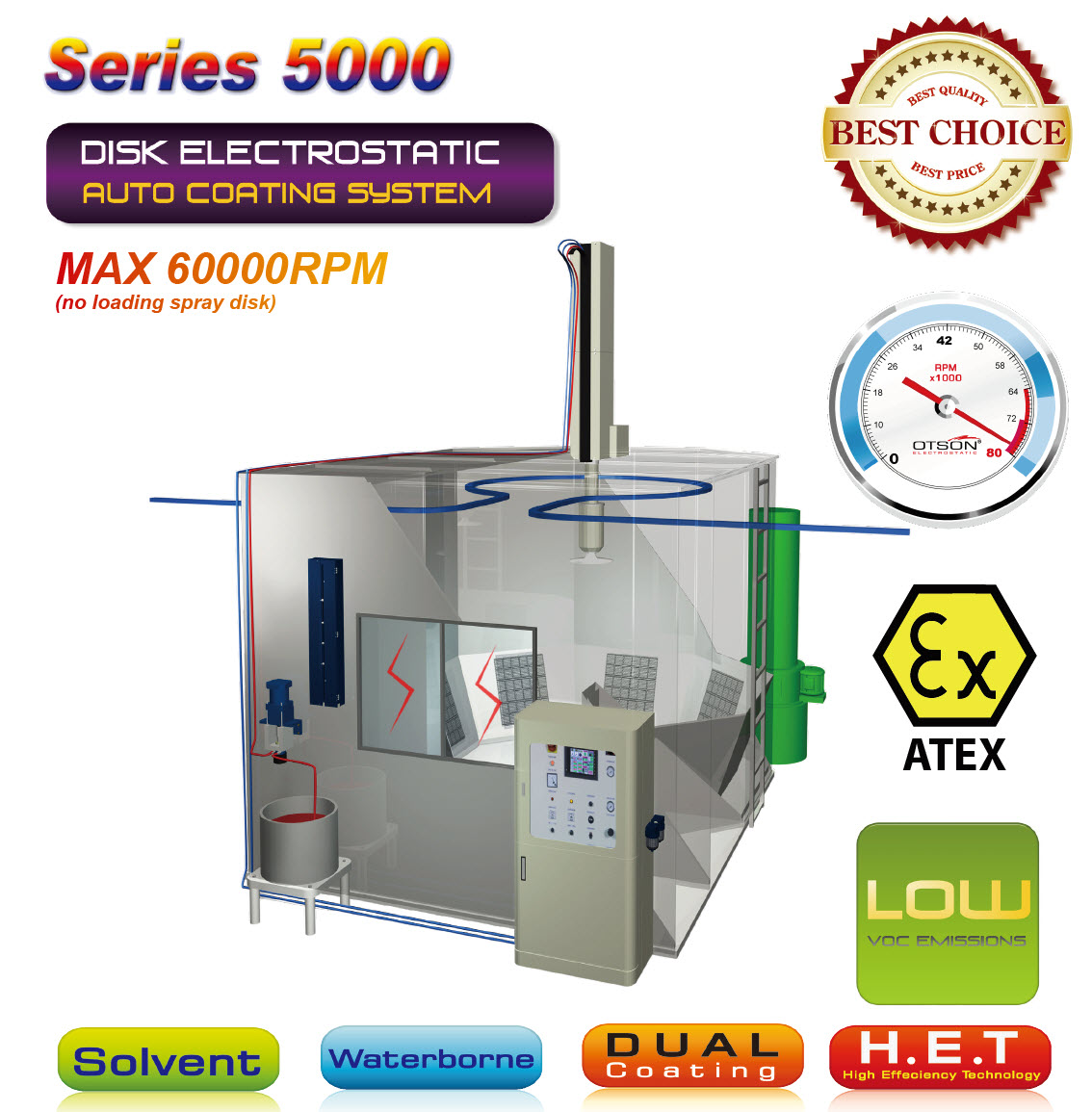
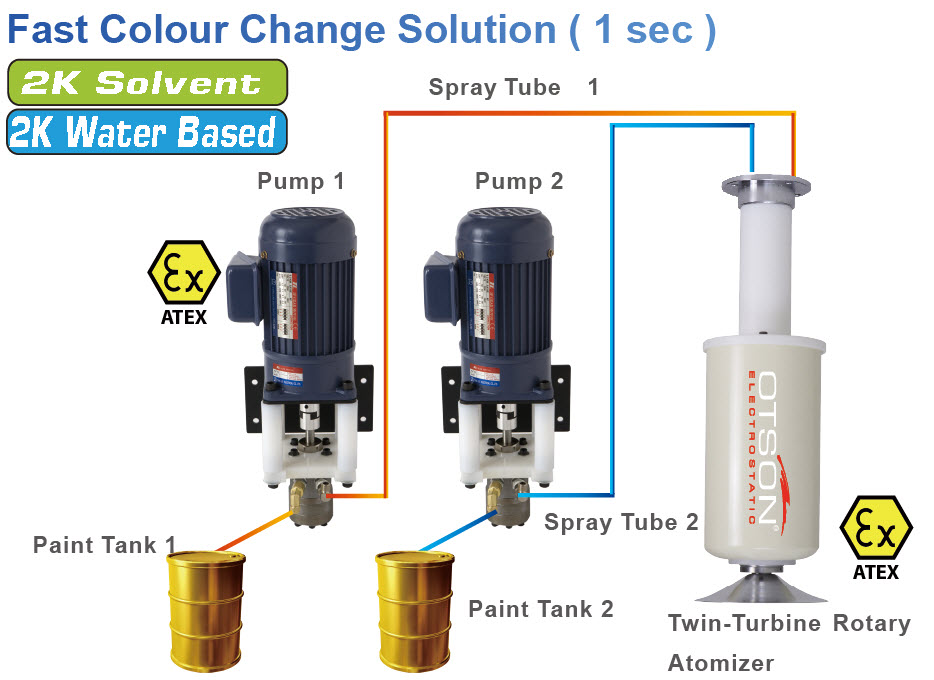
OTS-5000 -Disk ( Disc ) Electrostatic -Automatic Coating System
The OTSON auto electrostatic disc spray system is a state-of-the-art solution for coating and painting in potentially explosive environments. As a manufacturer of this system, it’s important to highlight its unique benefits to potential customers. Firstly, the system is safe and compliant, certified by Atex as the standard for equipment and protective systems intended for use in potentially explosive atmospheres.
In addition, the OTSON system provides faster coverage and increased production rates compared to traditional electrostatic spray guns. This, along with its ease of maintenance, makes it a reliable choice for industrial environments. The system can also handle a wide range of coatings and paints, including 2K and water-based paints, providing customers with greater flexibility and opening up new possibilities for their projects. Furthermore, the system is designed to reduce CO2 emissions and overspray, which can lead to cost savings and make it more environmentally friendly.
The Twin Turbine Atomizer is a key feature of the system, providing uniform coating thickness and fine atomization, reducing overspray and paint waste. The atomizer and discs also have quick-disconnect features, making maintenance easy and reducing downtime. The fully automated control panel allows for high production rates and reduced labor costs. Operators have total control flexibility and can change process parameters not only between batches but also within the same part. The simplified user interface can record ten different coating parameters, making it easier to apply coatings efficiently and effectively.
In summary, the OTSON auto electrostatic disc spray system is a cutting-edge solution for coating and painting in potentially explosive environments, providing faster coverage, ease of maintenance, and a wide range of capabilities. Its unique features, including the Twin Turbine Atomizer and fully automated control panel, make it a reliable and efficient choice for industrial environments.
Some of the key features of the OTSON auto electrostatic disc spray system include:
- Atex certification, suitable for use in potentially explosive environments.
- High rotary atomizer with smaller droplets for consistent and high-quality finish
- Larger capacity and ability to cover a larger area in a shorter amount of time than traditional electrostatic spray guns
- Easy maintenance
- Ability to handle a wide range of coatings and paints, including 2K and water-based paints
- Reduced CO2 emissions and overspray
- Twin Turbine Atomizer for fine atomization and uniform coating thickness
- Quick-disconnect features for easy maintenance and reduced downtime
- Automated control panel for high production rates and reduced labor cost
- Control flexibility allowing operators to change process parameters between batches and within the same part
- Simplified user interface control panel capable of recording ten different coating parameters
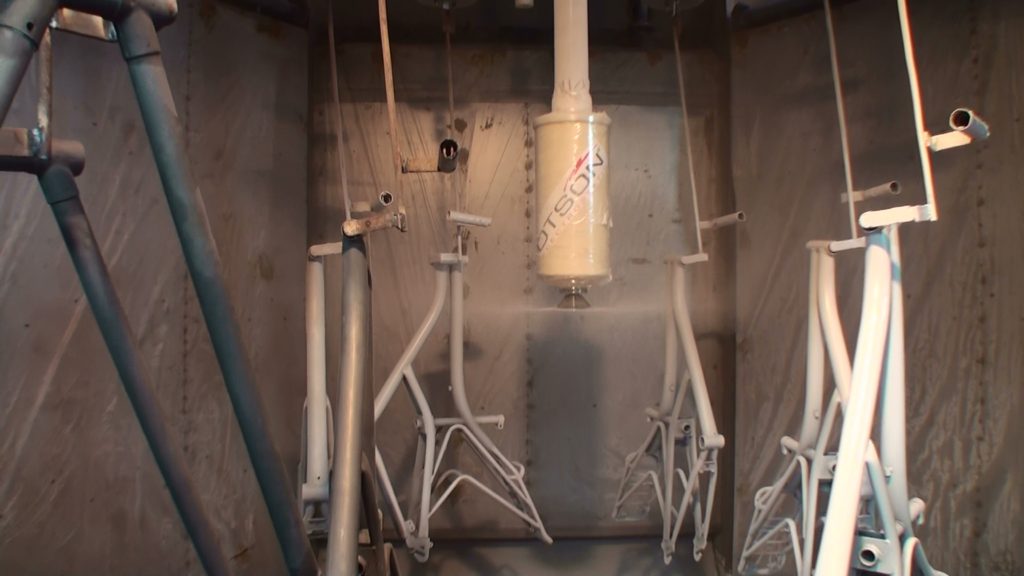
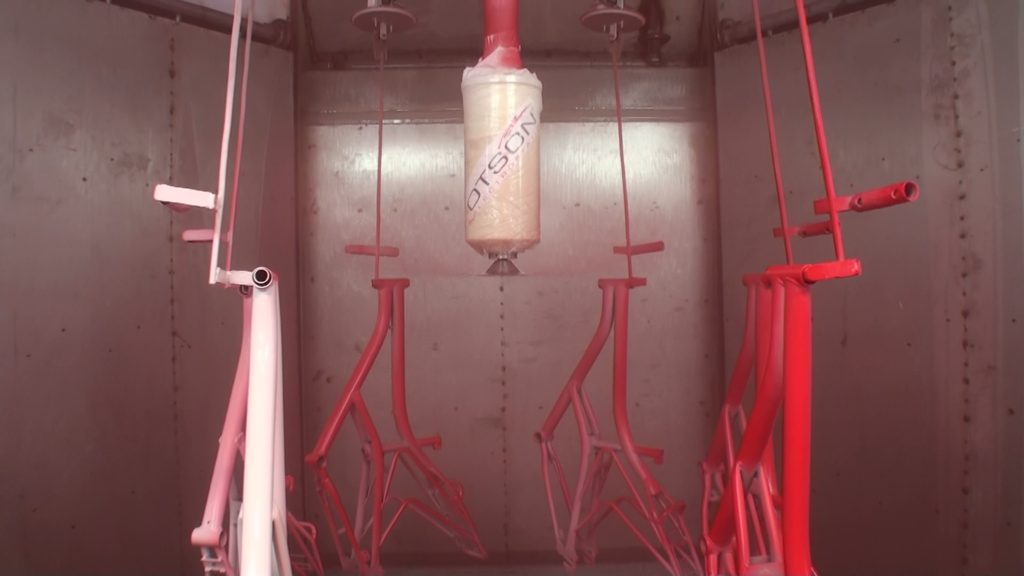
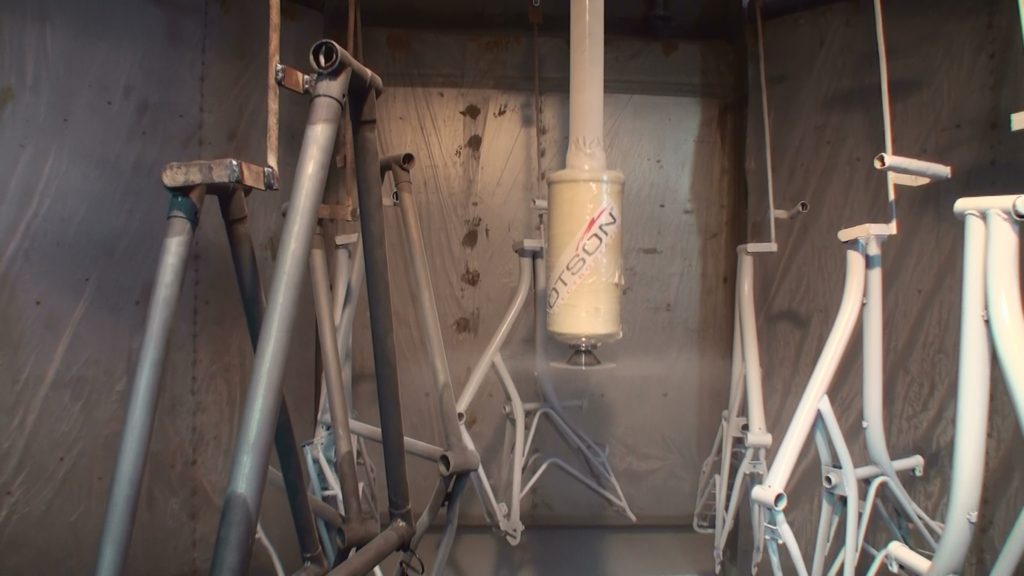
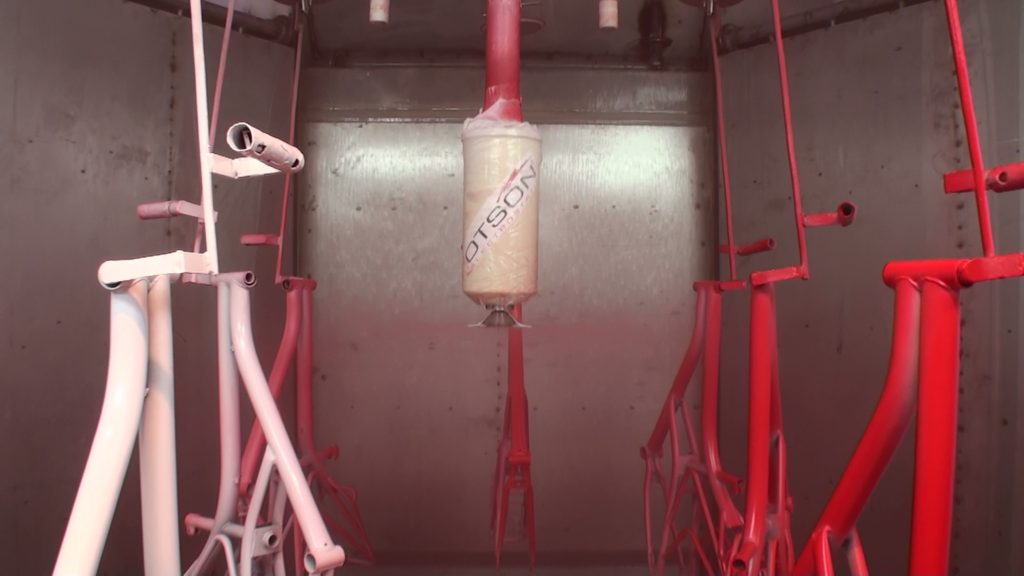
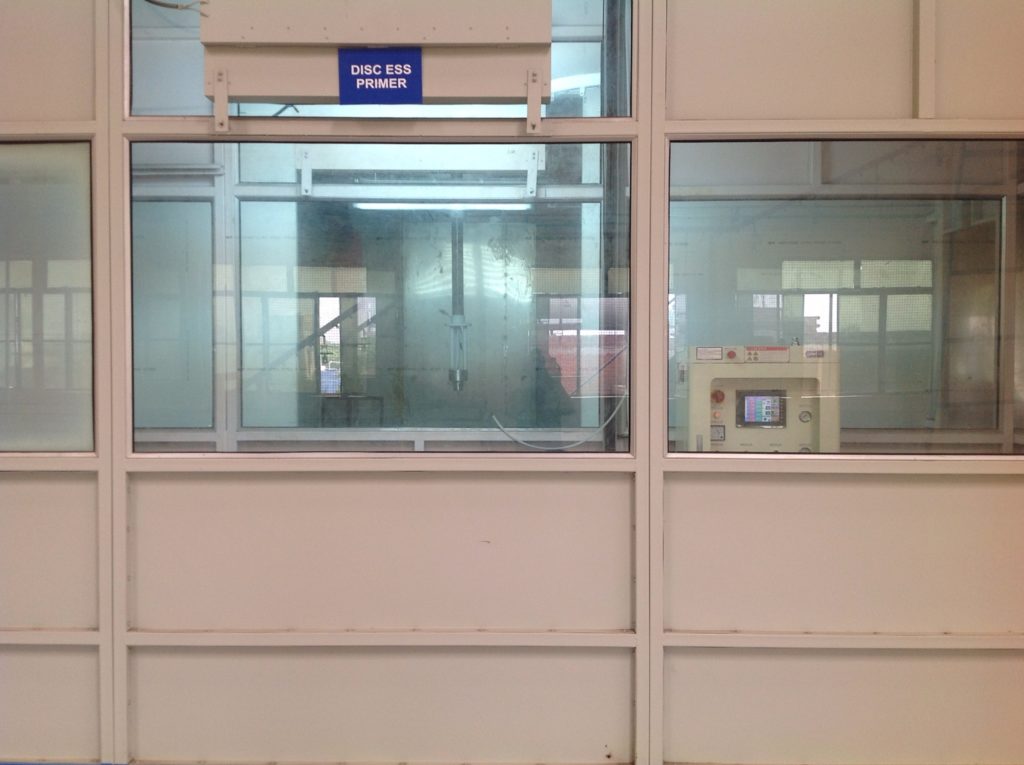
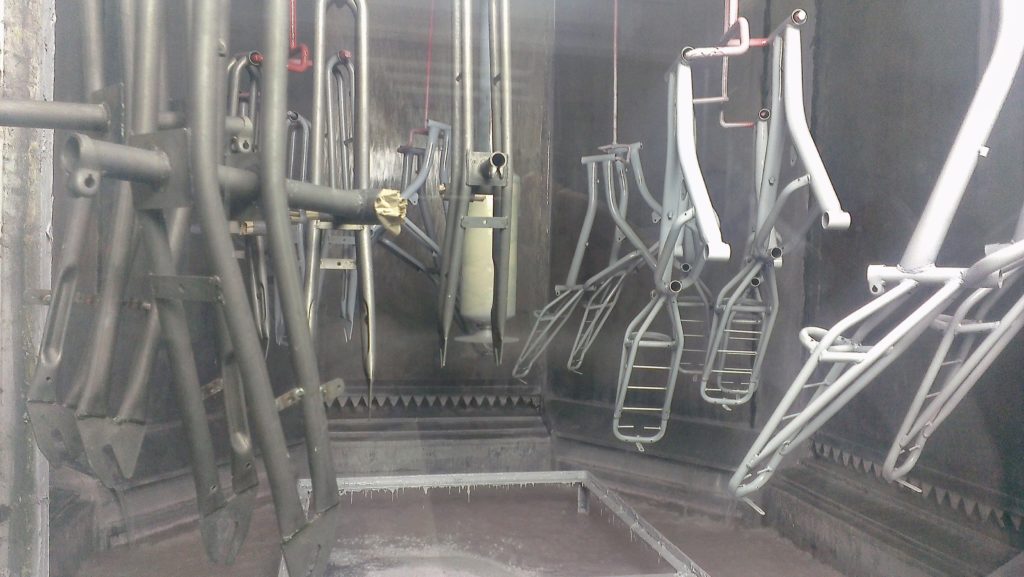
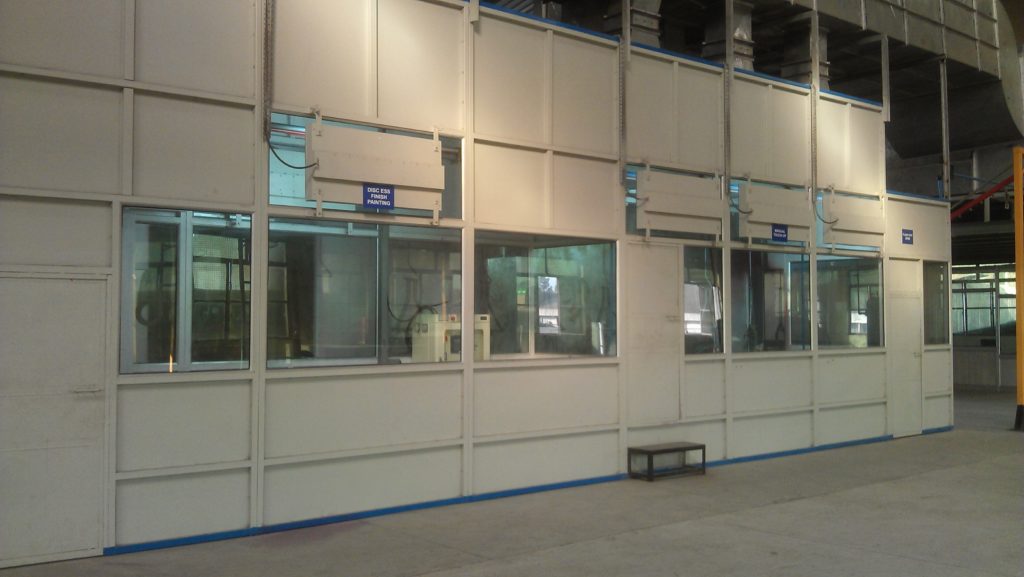
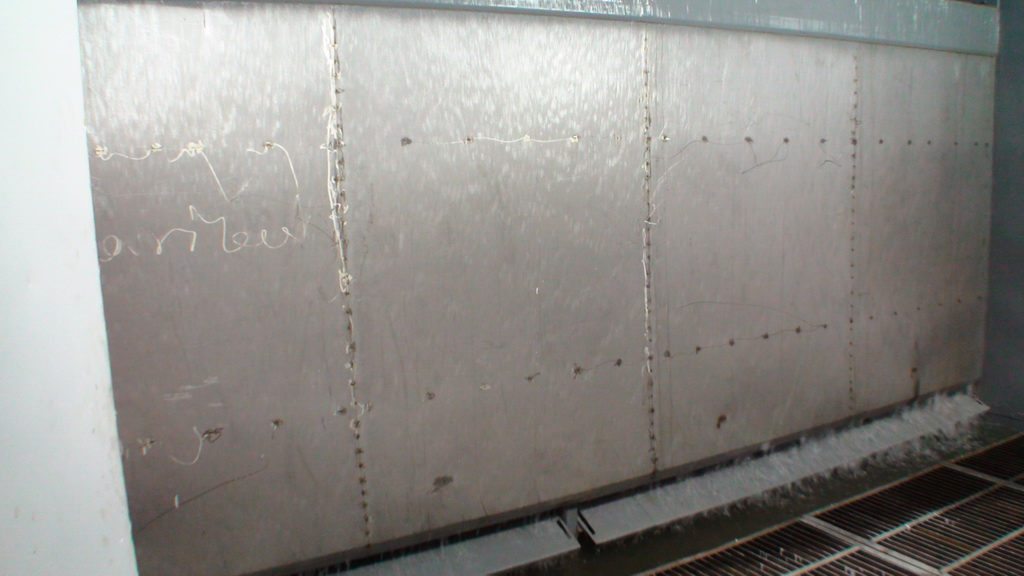
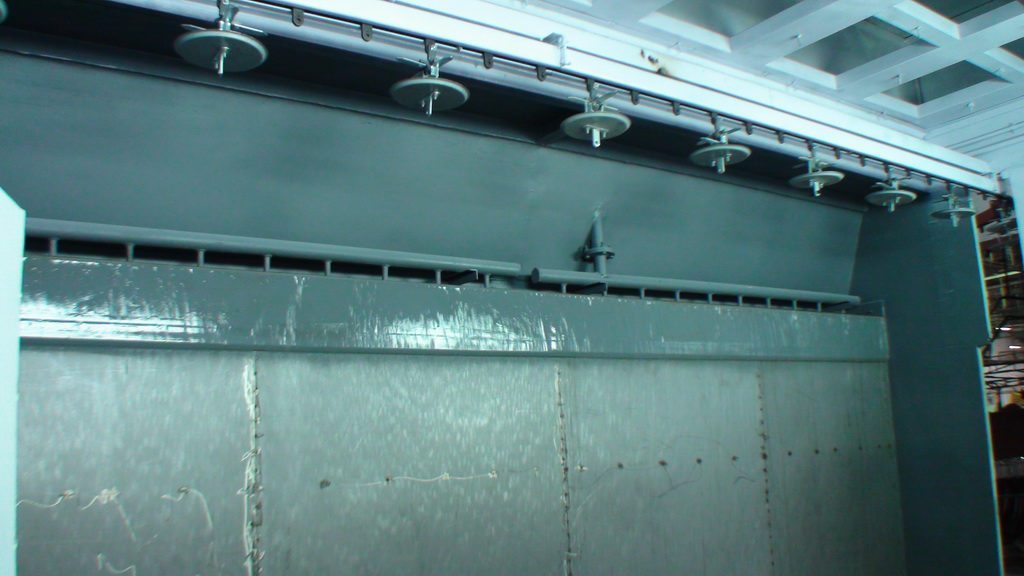
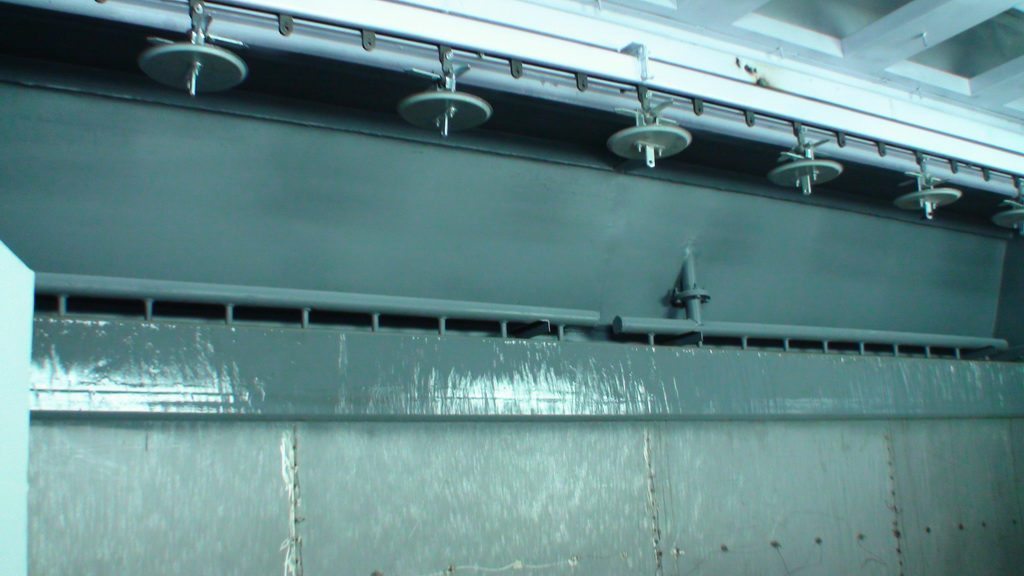
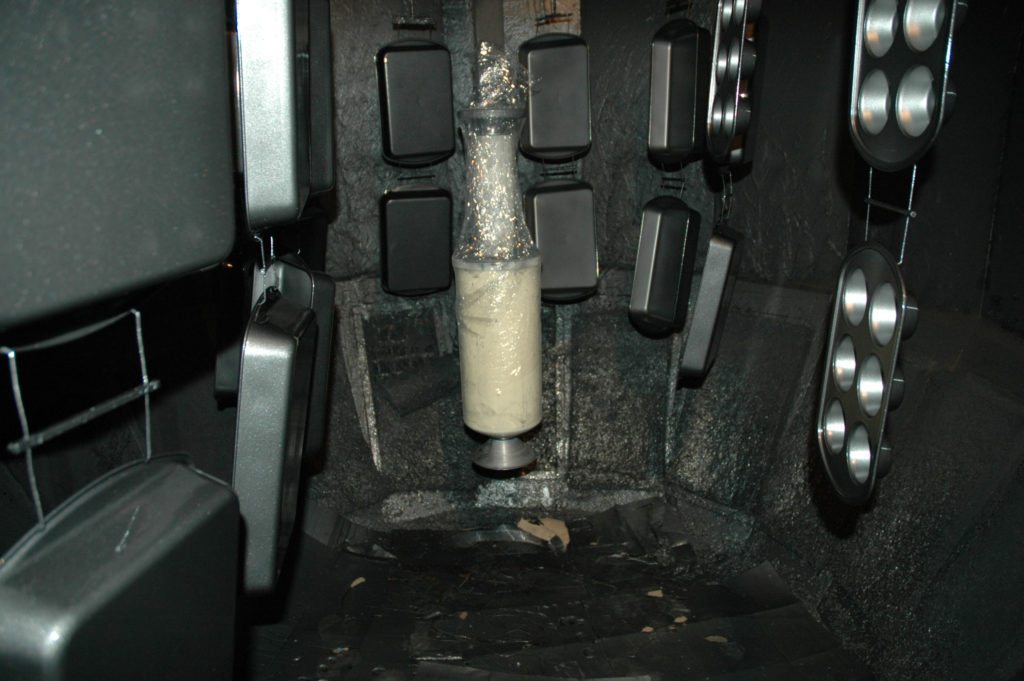
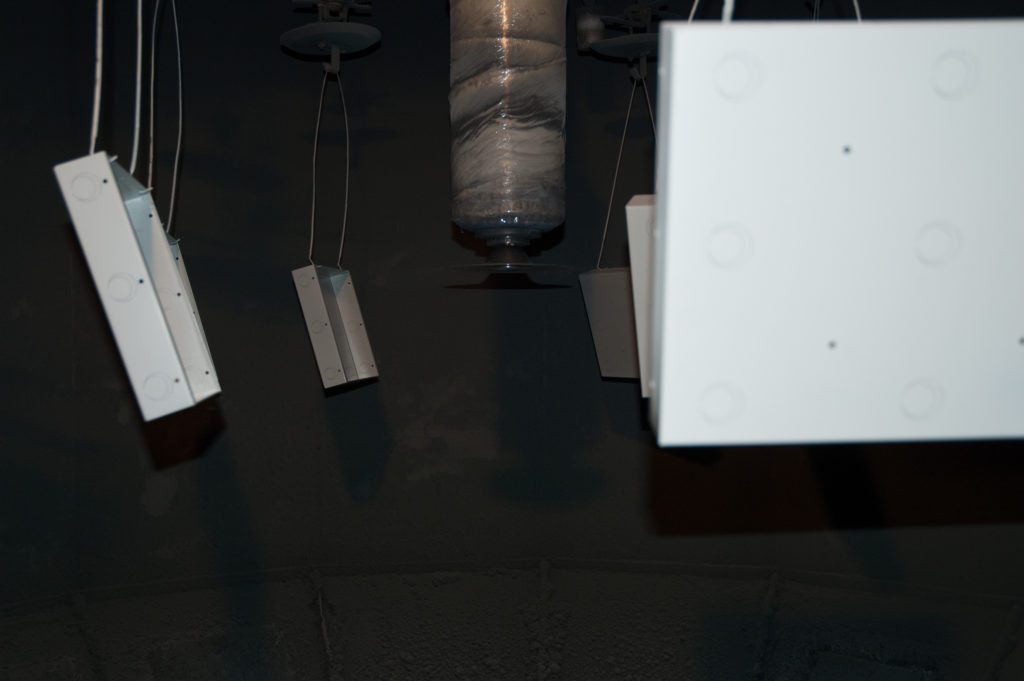
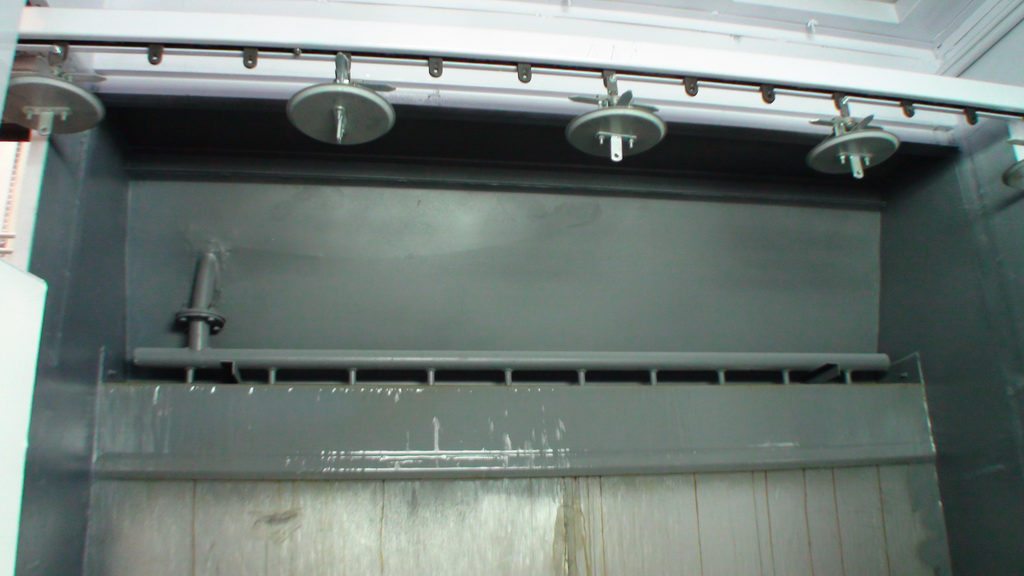
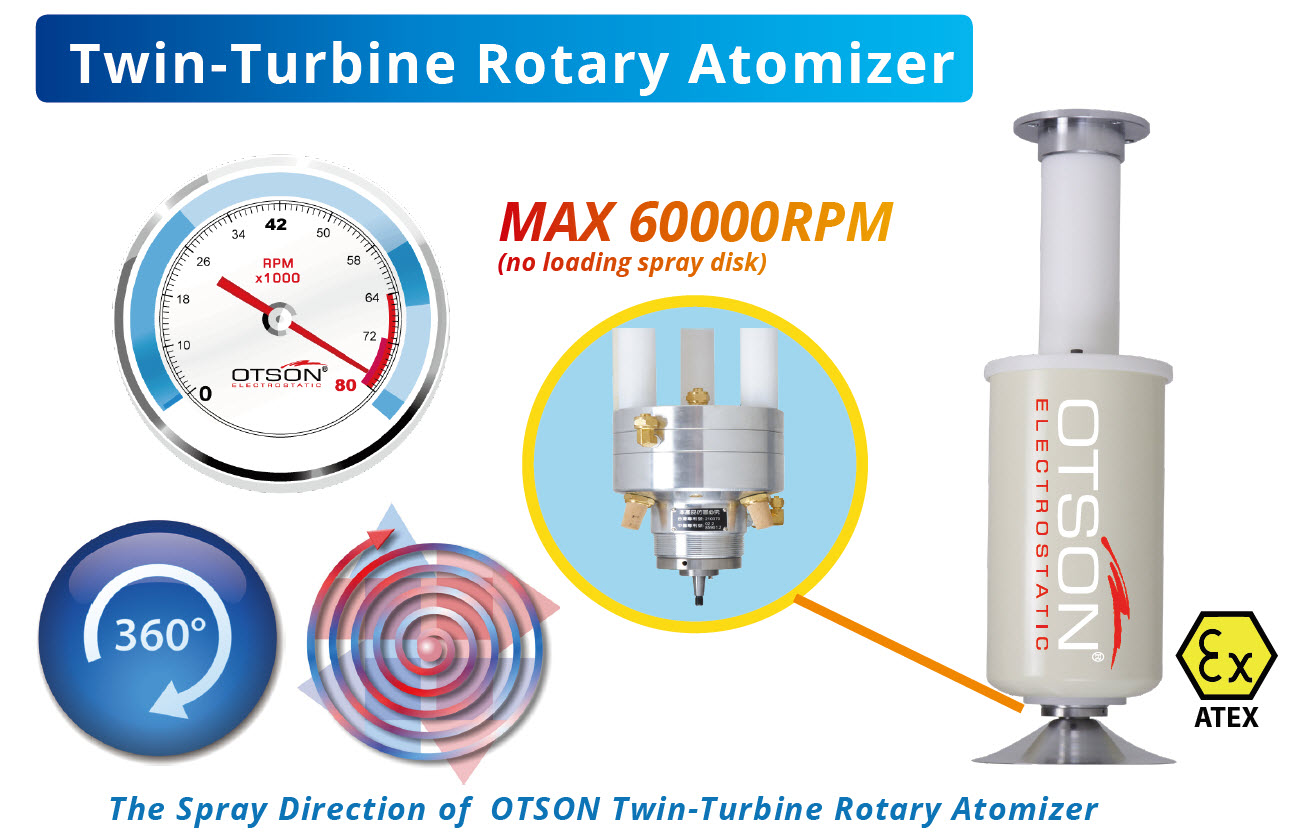
OTSON electrostatic high rotary atomizers are a cutting-edge solution for applying coatings and paints efficiently, with a high transfer efficiency that results in a higher quality finish. Our atomizers are designed to produce smaller droplets, which are more easily attracted to the grounded object, resulting in a more consistent and higher quality finish.
One of the key benefits of our OTSON high rotary atomizers is their ability to cover a larger area in a shorter amount of time than traditional electrostatic spray guns, which can result in increased production rates for your customers. Additionally, our atomizers are designed with easy maintenance in mind, making them a reliable choice for busy industrial environments. The atomizer can handle a wide range of coatings and paints, including those used in automotive, industrial, and marine applications.
As a manufacturer of OTSON electrostatic high rotary atomizers, we understand that every customer has different needs, and we are committed to providing the best solutions for their specific requirements. We have a team of experts ready to help them with the integration and optimization of our electrostatic high rotary atomizer in their processes.
Additionally, we have taken out a patent on the atomizing performance of our electrostatic high rotary atomizers, providing our customers with a unique and advanced solution for their coating needs. The high-speed rotation of our atomizers is capable of rotating at speeds up to 1,000 to 60,000 RPM, which is capable of atomizing even the toughest coatings into extremely fine particles to produce a high-quality finish.
Our Twin Turbine Atomizers fine atomization can provide uniform coating thickness on all surfaces, and relatively reduce overspray and paint waste. The quick-disconnect features of the Twin Turbine atomizer and the disks allow for easy maintenance and reduced downtime. Our control panel is fully automated and it provides high production rates and reduces labor cost. The control panel gives operators total control flexibility and allows the operator to change process parameters, not only between batches, but also within the same part. The simplified user interface control panel is capable of recording ten different coating parameters which is beneficial to apply in various objects easily and efficiently.
- Patent on atomizing performance
- High-speed rotation up to 1,000 to 60,000 RPM
- Twin Turbine Atomizer for fine atomization and uniform coating thickness
- Quick-disconnect features for easy maintenance and reduced downtime
- Automated control panel for high production rates and reduced labor cost
- Control flexibility allowing operators to change process parameters between batches and within the same part
- Simplified user interface control panel capable of recording ten different coating parameters
- Larger capacity and ability to cover a larger area in a shorter amount of time than traditional electrostatic spray guns
- Easy maintenance and ability to use a wide range of coatings and paints for various applications
- High-quality finish with consistent and even application, reducing overspray and paint waste.
A comparison of Single Disc and S-Type liquid electrostatic spray systems in terms of the following aspects:
- Atomization: Single Disc systems use a spinning disc to atomize the liquid coating material and create an electrostatic charge on the coating particles, while S-Type systems use a spinning disc in combination with an electrode to charge the atomized particles.
- Precision and Control: S-Type systems are considered more precise and controlled in terms of coating application, making them better suited for larger or complex-shaped objects.
- Transfer Efficiency: S-Type systems have a higher transfer efficiency, typically around 85-97%, compared to Single Disc systems which have transfer efficiencies of around 80-90%. This can lead to improved coating uniformity and reduced material waste, resulting in increased production rates.
- Cost: Single Disc systems are typically less expensive to purchase and maintain than S-Type systems. However, the cost savings from reduced material waste and increased production rates provided by S-Type systems may offset the initial cost.
- Suitable Applications: Single Disc systems may be a cost-effective solution for certain liquid coating applications, and can provide good coating quality, but may not be as precise as S-Type systems, and may not be suitable for larger or complex-shaped objects. S-Type systems are suitable for larger or complex-shaped objects and will provide a higher precision and controlled coating application.
It’s important to note that both Single Disc and S-Type systems use electrostatic power to attract the liquid coating material to the surface being coated. The main difference is in the atomization process and the level of precision and control in the coating application, with S-Type systems being more precise and controlled.
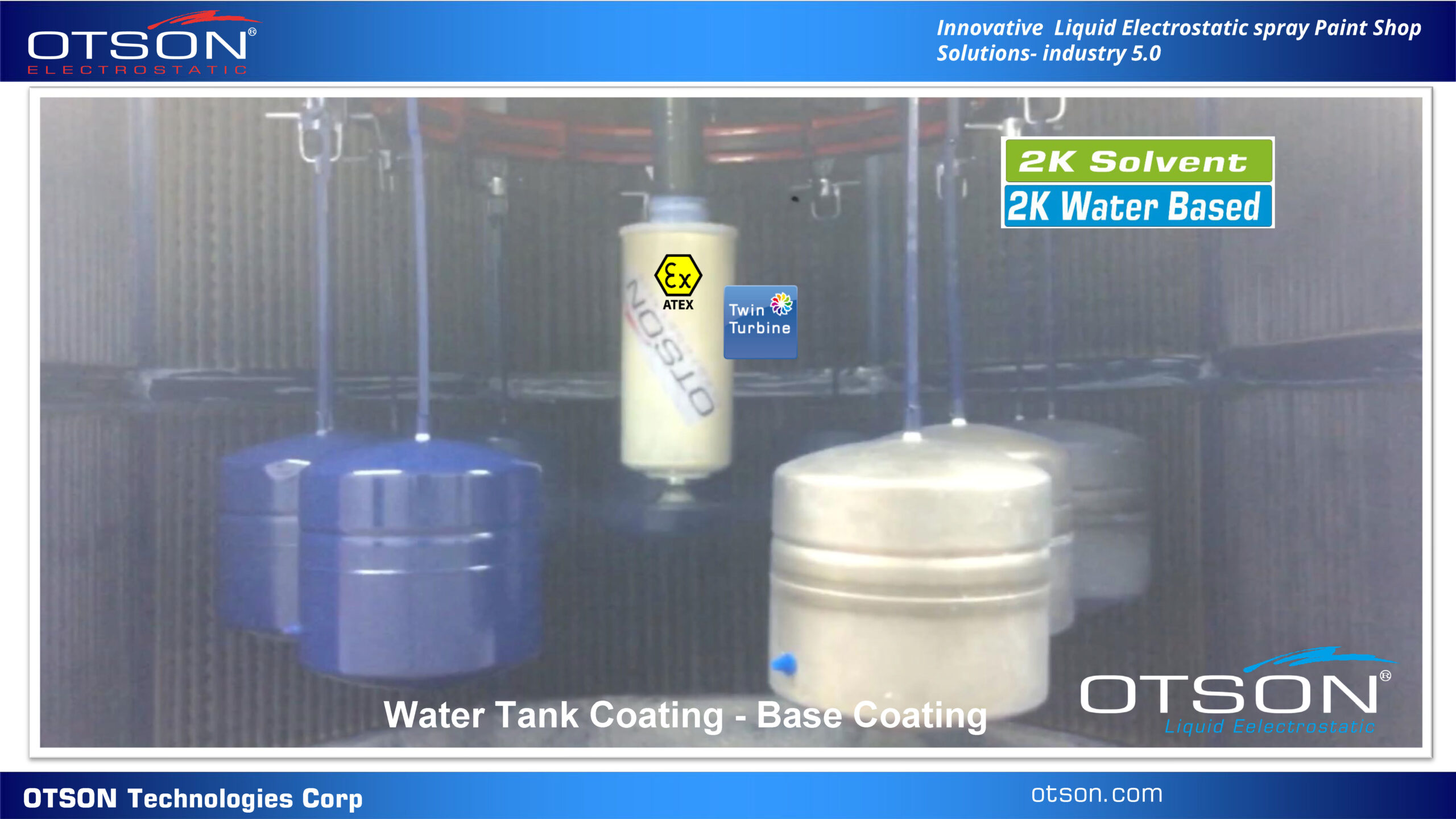
The electrostatic effect of the Auto Disk (Disc) electrostatic spray system with twin-turbine atomizer is a process where a charged liquid coating material is atomized into small droplets by the twin-turbine atomizer. The vertical type system is designed to optimize the electrostatic charging of the droplets as they are propelled towards a grounded object or surface.
The system works by creating a high-velocity air stream, which entrains the liquid coating material and atomizes it into fine droplets. The twin-turbine atomizer then uses an electrical charge to further separate the droplets and give them a charge. This charge creates an attractive force between the charged droplets and the grounded object, which allows for a more efficient and uniform application of the coating material.
The electrostatic effect of the Auto Disk (Disc) electrostatic spray system provides several benefits to the customer, including improved efficiency and transfer efficiency, reduced material waste, and reduced operator fatigue. This system also provides for a more consistent and uniform coating, as well as a reduction in the amount of overspray.
It is important to note that the electrostatic effect of the Auto Disk (Disc) electrostatic spray system is dependent on the specific conditions and materials being used, so the exact results may vary depending on the application. However, this system provides an effective and efficient solution for many industrial coating applications, and can help to improve the quality and efficiency of the coating process.
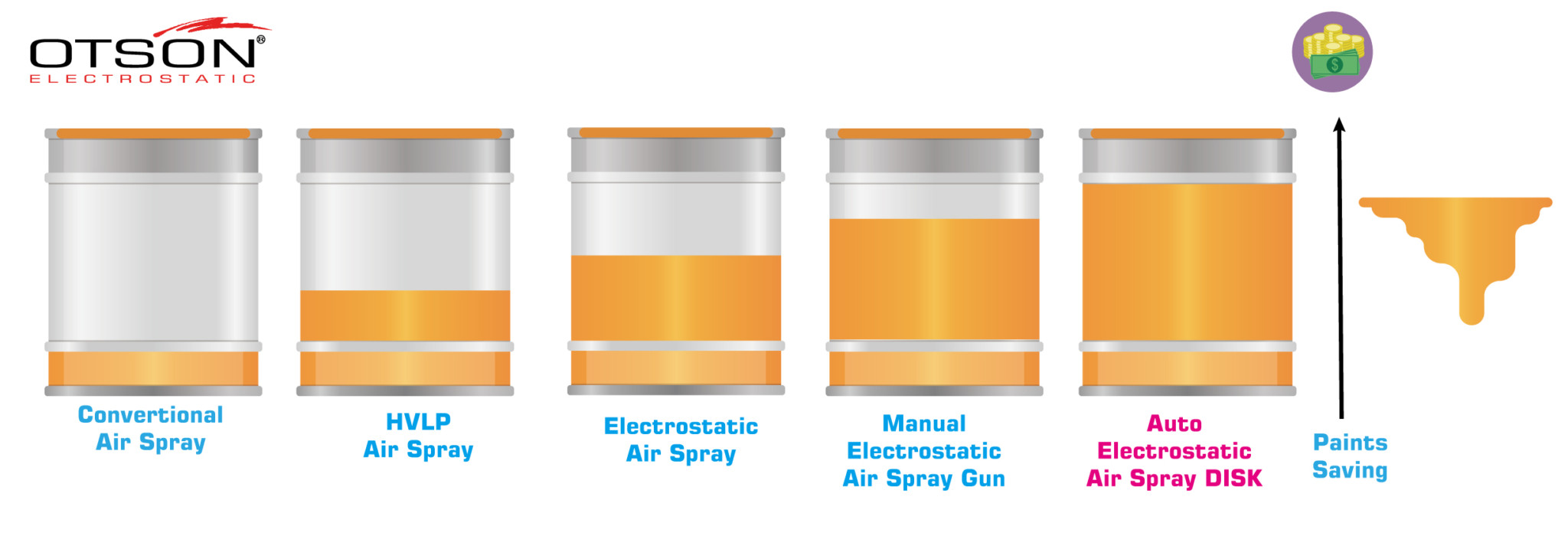
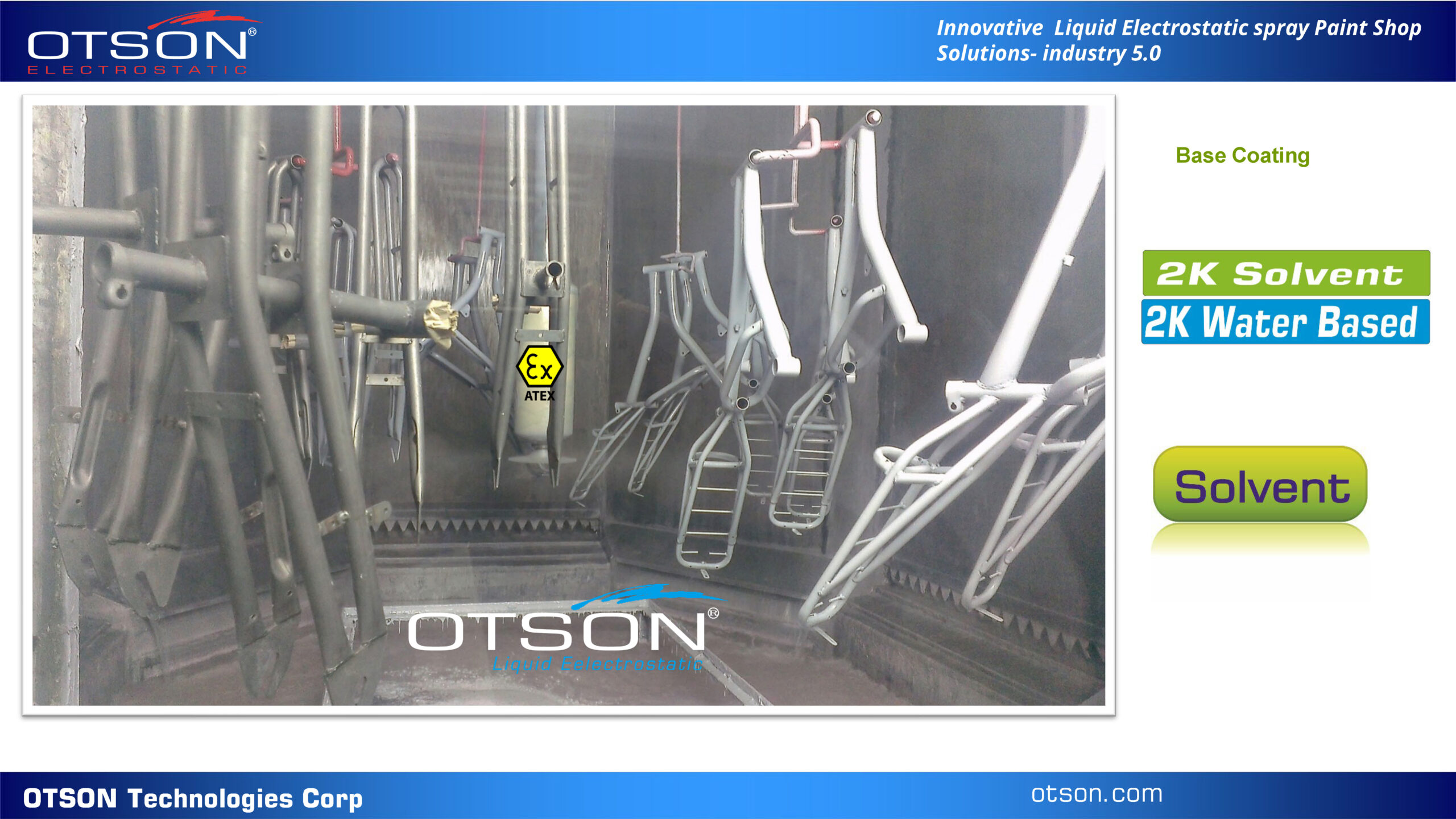
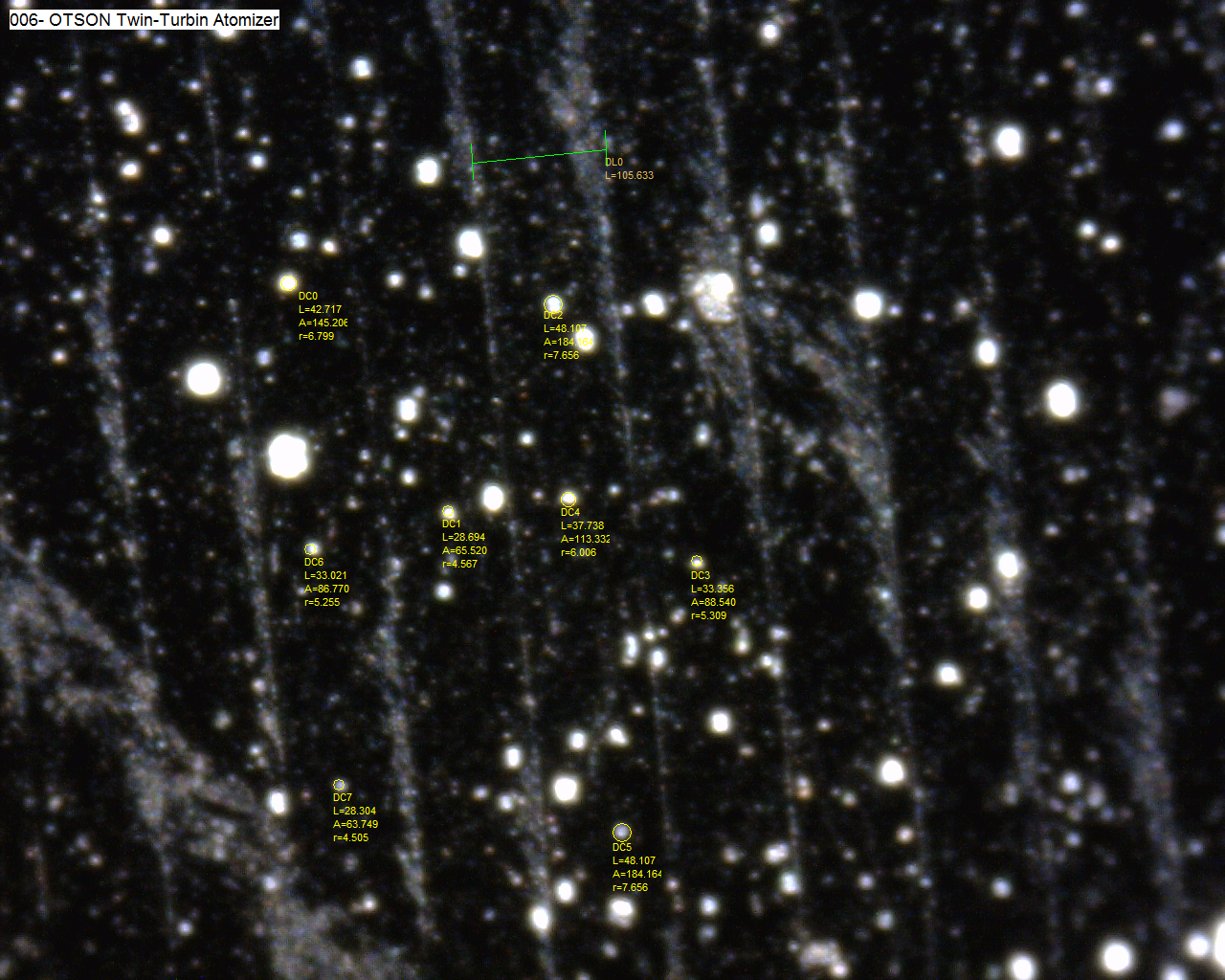
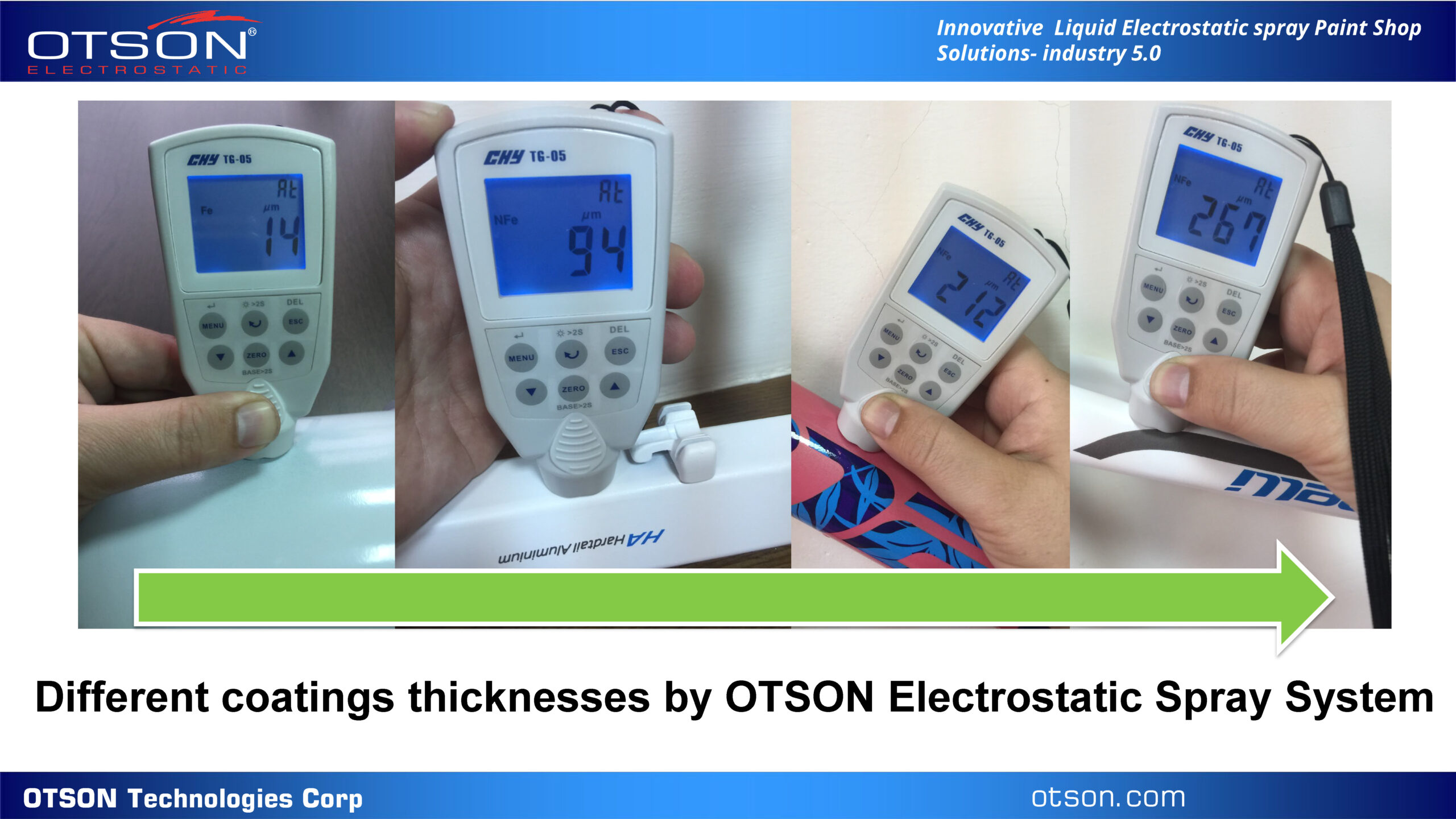

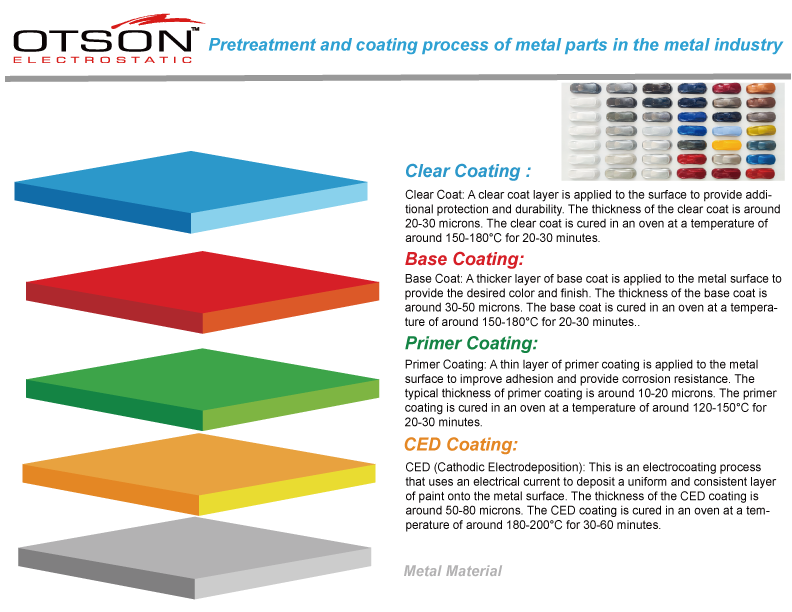
-
Automotive: cars, trucks, buses, motorcycles, and other vehicles.
-
Aerospace: airplanes, helicopters, satellites, and other aircraft.
-
Manufacturing: industrial equipment such as machinery, conveyor systems, tanks, and other metal structures.
-
Marine: ships, boats, yachts, and other watercraft.
-
Furniture: chairs, tables, cabinets, and other furniture pieces.
-
Medical: medical equipment such as MRI machines, X-ray machines, and surgical instruments.
-
Appliance: household appliances such as refrigerators, ovens, dishwashers, and other large appliances.
-
Agricultural: farm equipment and machineries, such as tractors, plows, and harvesters.
-
Construction: buildings, bridges, and other structures such as towers and cranes.
-
Electrical: electrical equipment and devices such as transformers, switchgear, and other high voltage equipment.
-
Sporting Goods: bicycles, exercise equipment, and other sports-related items.
-
Signage: signs, billboards, and other forms of advertising.
-
Retail: store fixtures, displays, and other items found in retail settings.
-
Food & Beverage: food processing and packaging equipment, beverage dispensing equipment, and other items found in food and beverage manufacturing facilities.
-
Small parts: gears, bolts, and other small metal components.
-
Bicycle: frames, forks, and other components of bikes.
-
Computer housing: exterior of computer towers, monitors, and other electronic devices.
-
Stationeries: pens, pencils, and other writing instruments.
-
Wooden furniture: wooden chairs, tables, and other pieces of furniture.
-
Hardware: locks, knobs, and other hardware items.
-
Lockers: exterior of metal lockers.
-
Freezers: exterior of commercial freezers and refrigeration units.
-
Iron railing: exterior of iron railings, fences, and other metal structures.
-
Major Appliances: washing machines, dryers, and other large household appliances.
-
Office equipment: printers, copiers, and other office machines.
-
Desks: exterior of desks and other office furniture.
-
Files: exterior of metal file cabinets and storage units.
-
Office partitions: exterior of office partitions and dividers.
-
Medical Equipment: surgical instruments, x-ray machines, and other medical devices.
-
Metal doors: exterior of metal doors, including commercial and industrial doors.
-
Car accessories: mirrors, spoilers, and other aftermarket car parts.
-
Teflon pots: exterior of Teflon-coated pots and pans.
-
Musical instruments: guitars, pianos, and other musical instruments.
-
Environmental equipment: air purifiers, water filtration systems, Water Tanks, and other environmental equipment.
-
Plastic products: plastic toys, bottles, and other plastic products.
-
Metal products: metal signs, metal sculptures, and other metal products.
-
Glass products: glass bottles, windows, and other glass products.
-
Military:
-
Wind Power :