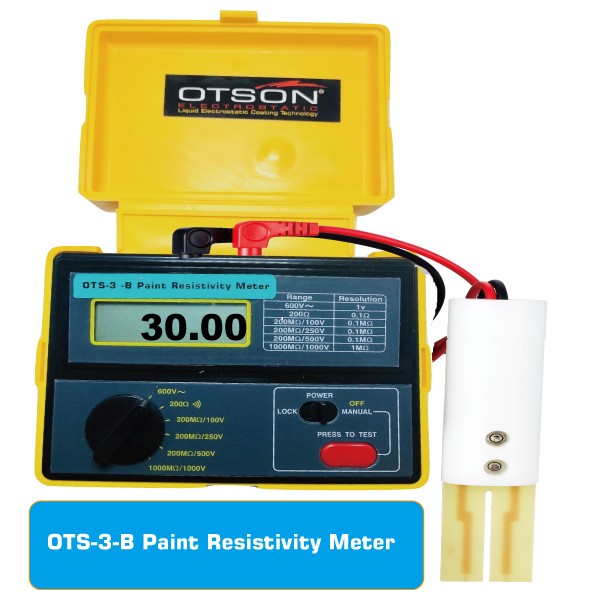
- Digital display, easy and correct read-out.
- Multi function for insulation measurement of 200 M ohm(100V) 200 M ohm(250V), 200 M ohm(500V), 1000 M ohm(1000V).
- Build in the ACV & OHM measurement function.
- Precision 200ohm range easy for measuring low resistance such as motor windings, relay coils etc.
- A continuity beeper is equipped in 200 ohmrange.
- Insulation measurement with high drive current,2.8 mA short circuit current.
- 18mm (0.7″) large LCD display.
- Battery operating easily to carry with user.
- LCD display allows clear read-out even at bright place.
- LSI-circuit provides high reliability and durability.
- Built-in over-input and low battery indication.
- Overload protection for each range.
- Automatic zero adjust & automatic circuit discharge.
- Durable & portable housing case with the front protective cover.
- General Coatings
- PU coatings
- Water leather coatings
- UV special coatings
- Liquid coatings
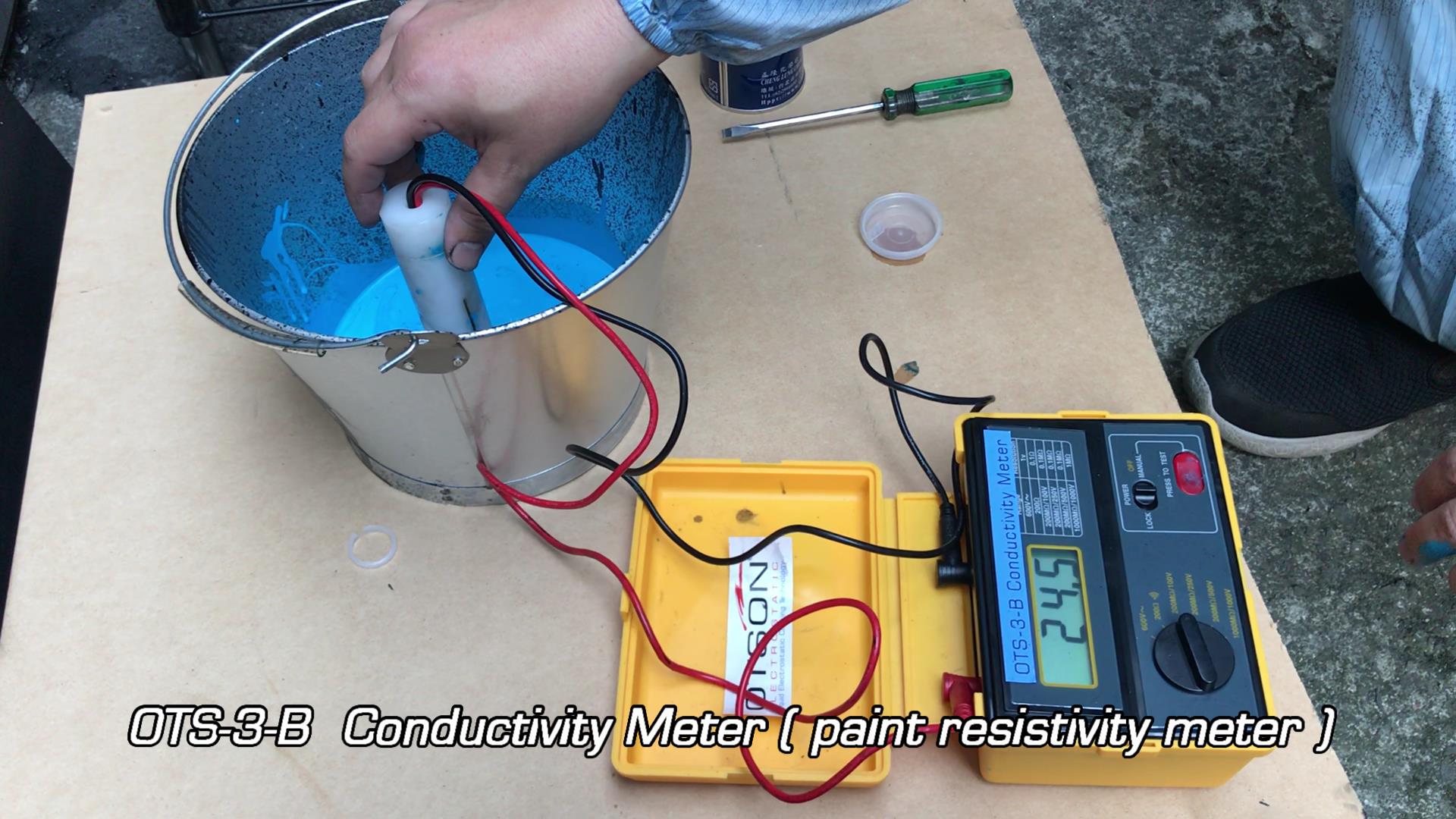
- Too much or too little resistance of the coating will affect the operation of the electrostatic spray equipment . If the resistance of the coating is too large , the charging rate is low during the spraying process, and the conductivity is good. After the coating with small resistance is charged, the electric charge disappears too fast, and the static voltage does not go up, which also affects the spraying effect.
- When the conductivity of the coating is too strong, the current intensity of the system is large, and the electrostatic spray coating effect is poor, and the paint mist particles cannot fall on the surface of the coated workpiece to affect the coating effect. Studies have shown that some coatings are easy to charge, and some are not easy to be charged. This has a lot to do with the nature of the resin in the coating. For example, melamine resin has good conductivity, alkyd resin has certain conductivity, and epoxy resin. Poor conductivity. The color and solvent properties of the coating also have a large effect on the conductivity of the coating. The conductivity of a pigment is related to its particle shape in addition to its nature. Generally, the finer the particle, the better the conductivity, so the pigment of the diamond particle and the spherical particle is finely ground. Coatings generally do not produce coatings that are used directly for electrostatic spraying, but can provide solvents that are added to the coating during electrostatic spraying. Adding these solvents to ordinary coatings can turn them into coatings for electrostatic spraying. Electrostatic spraying should use easy-to-charge coatings. Generally, the resistivity is 5~50MΩ·cm. For coatings with poor electrical conductivity above 100MΩ, a polar solvent (such as diacetone alcohol) should be added to improve the coating. Conductivity, but should pay attention to the amount of addition should be appropriate, more will affect the coating’s hiding and durability. Coatings with too low resistivity such as water-based paints and metallic flash paints require a non-polar solvent to increase their electrical resistance.
- Metal powder has strong electrical conductivity. By adding a non-polar solvent to surround the metal powder particles, it can reduce its conductivity, but this segmentation is closely related to the shape of the metal particles, and there is no sharp corner. The round particles are more easily surrounded by the segmentation. After the application of high voltage, the metal powders are not connected to form a conductive path, but if the metal particles have sharp corners and are used in a non-circulating electrostatic spraying system, It is easy to break through the separation of the solvent to form a conductive path, and the more sharp the corners, the easier it is to form a conductive path. Therefore, when the metal paint is electrostatically sprayed, not only a non-polar solvent but also a circulation system should be used. At the same time of coating the impedance, it is also necessary to balance the leveling property of the coating, that is, with a high boiling point solvent, to control the proper evaporation rate of the solvent, to achieve a better leveling, and to improve the decorativeness of the coating.
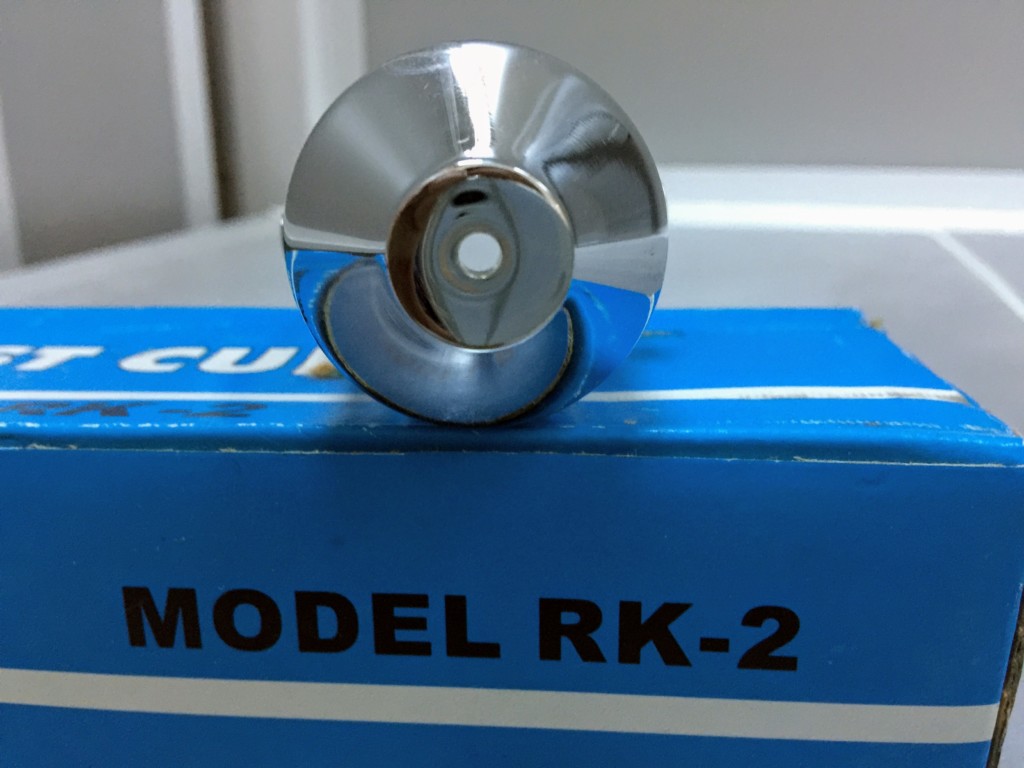
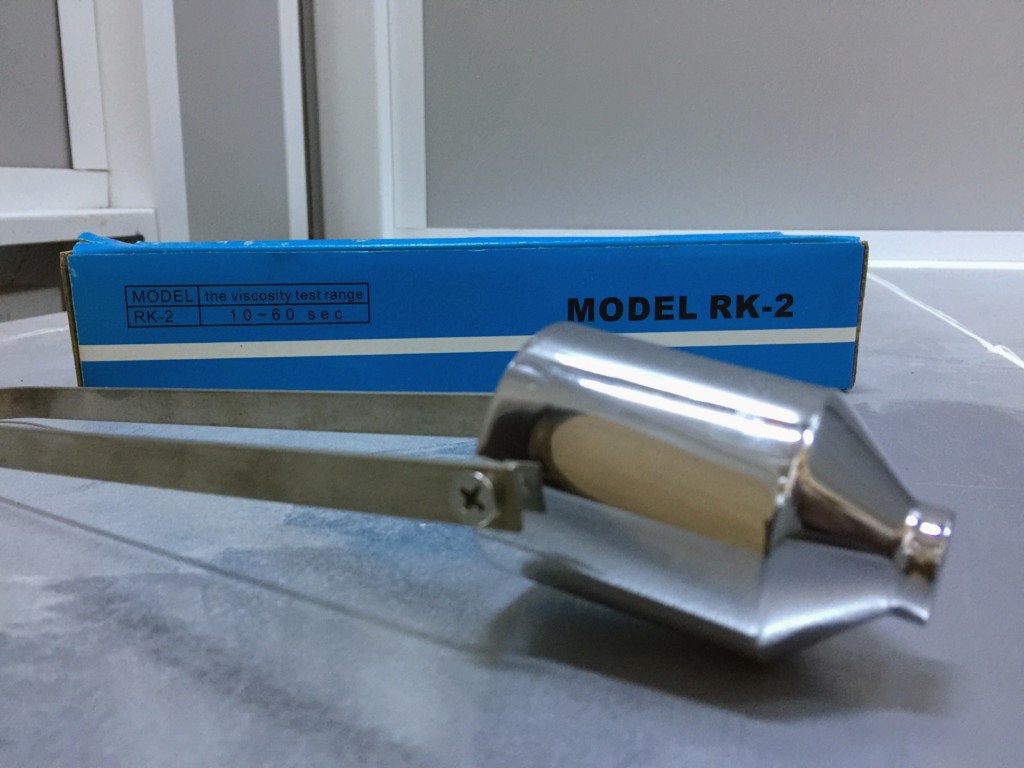
For all OTSON electrostatic spray equipment,A paint impedance should be between 20M ohm to 30 M ohm to obtain an appropriate charge. Changes can be made to make a coating more conductive, including solvent additions, changes in solvent composition, and the use of polar solvents. Viscosity corrections may also need to be made to ensure coating droplets are fine enough.
The conductivity of the paint, or its capacity to carry an electrical charge, is an important factor in electrostatic spraying. The paint to be used should be conducive enough to accept the negative charge from the spray gun but not so conductive that the charged paint tracks back to the ground through the paint system supply. Water-bourne and metallic coatings tend to be highly conductive, while solvent coatings tend to be non-conductive. Paints can be modified with a polar solvent (e.g., alcohols and ketones) or conductive pigments (e.g., metallic pigments) to increase their conductivity. Likewise, highly conductive coatings can be modified to prevent the electrical charges from shorting to the ground and leaving the paint uncharged.
Paint throughput and coating quality are influenced by viscosity, surface tension, conductivity, solvent evaporation, etc., the type of atomizing equipment, and by the way the equipment is controlled.
An electrostatic spray system should balance paint particle velocity and electrostatic voltage to optimize coating transfer efficiency. CONDUCTIVITY PROMOTER or pigments
- Solvent-borne: Coatings in which VOCs are the major solvent or dispersant.
- Polar: Descriptive of molecules where the atoms and their electrons and nuclei are arranged so that one end of the molecule has a positive electrical charge and the other end of the molecule has a negative electrical charge. The greater the distance between the two charged ends, the higher the polarity. Polar molecules ionize in solution and impart electrical conductivity.
- Viscosity: The property of a fluid whereby it tends to resist relative motion within itself. A thick liquid such as syrup has a high viscosity. Viscosity is often measured using an efflux-type cup, which gives the time required for a given quantity of paint to flow through a hole in the bottom of the metal cup at a given temperature (See Zahn or Iwata NK-2 Cup).
Electrostatic spraying is a method of applying coatings that uses an electrostatic charge to attract the coating material to the surface being coated. This method allows for a more precise and efficient application of the coating, as the electrostatic charge helps to ensure that the coating particles are attracted to the surface and adhere evenly.
However, in order for the electrostatic spraying process to work effectively, the coating material must have the right conductivity. If the coating has too much resistance, it will not charge properly and the spraying process will be inefficient. On the other hand, if the coating has too little resistance, the charge will dissipate quickly and the spraying process will also be ineffective. Therefore, it’s important to use a coating material that has the appropriate resistance or conductivity level for electrostatic spraying.
Different types of resins used in coatings have varying conductivity levels. Melamine resin has good conductivity, while epoxy resin has poor conductivity. The properties of the color and solvent used in the coating also affect its conductivity. Pigment particle shape also plays a role, with finer particles generally having better conductivity. To obtain an optimal spraying effect, the coating material should have a resistance or conductivity level between 20M ohm to 30 M ohm.
Water-based coatings are typically highly conductive and can cause problems in the electrostatic spraying process because they can track back to the ground through the paint system supply. To overcome this issue, one solution is to add a small amount of a non-polar solvent to the paint, which increases its resistance and prevents it from tracking back to the ground. Another solution is to use specially formulated water-based paints that have a higher resistance level. Additionally, some electrostatic spray equipment is specifically designed to work with water-based paints and can help mitigate this problem.
In case of metal paint, metal powder has high conductivity, so it is important to use non-polar solvent and a circulation system to reduce its conductivity. However, the shape of the metal particles also plays a role. If the metal particles have sharp corners, they are more likely to form a conductive path in non-circulating systems, making it difficult to achieve a proper electrostatic charge. Therefore, using a non-polar solvent and a circulation system is necessary to reduce the conductivity of metal paint while spraying.
So the key point is, The electrostatic spraying process is highly dependent on the conductivity of the coating material and the resistance it has, this can be affected by the type of resin, properties of color, solvents and particle shape. Additionally, water-based paint have a specific conductivity problem, but have solutions and techniques to overcome that as well as conductivity of metal paint also should be taken care of while spraying
Paints Type | Paints Type |
Melamine Coatings | Car ,Boat ,Metal |
Polyester-melamine | Furniture, electrical equipment, car wheel,bicycle,Computer case |
Polypropylene Coatings | Wooden, Furniture |
Poly Urethane Coatings | Motorcycle ,bicycle , Car,medical equipment , Machine |
Polyurethane Coatings | Wooden, Metal , Leather, Plastic, Furniture |
NC Lacquer | Wooden, Metal, Furniture |
Metallic luster Coatings | Wooden, Metal, Furniture |
Water Soluble Paint | Wooden, Metal, Furniture |
- Electrostatic spraying: This is a method of applying coatings that uses an electrostatic charge to attract the coating material to the surface being coated. This method allows for a more precise and efficient application of the coating, as the electrostatic charge helps to ensure that the coating particles are attracted to the surface and adhere evenly.
- Conductivity of the coating material: The resistance of the coating material is a crucial factor when it comes to electrostatic spraying. If the resistance of the coating is too high, the charging rate is low during the spraying process, and the conductivity is good. After the coating with small resistance is charged, the electric charge disappears too fast, and the static voltage does not go up, which also affects the spraying effect.
- Different types of resins: Studies have shown that some coatings are easy to charge, and some are not easy to be charged. This has a lot to do with the nature of the resin in the coating. For example, melamine resin has good conductivity, alkyd resin has certain conductivity, and epoxy resin. Poor conductivity.
- Properties of color and solvents : The color and solvent properties of the coating also have a large effect on the conductivity of the coating. The conductivity of a pigment is related to its particle shape in addition to its nature.
- Water-based paint conductivity : Water-based coatings are typically highly conductive and can cause problems in the electrostatic spraying process because they can track back to the ground through the paint system supply. To overcome this issue, one solution is to add a small amount of a non-polar solvent to the paint, which increases its resistance and prevents it from tracking back to the ground. Another solution is to use specially formulated water-based paints that have a higher resistance level. Additionally, some electrostatic spray equipment is specifically designed to work with water-based paints and can help mitigate this problem.
- Metal paint conductivity : Metal powder has high electrical conductivity, and using a non-polar solvent to surround the particles can reduce its conductivity. However, the shape of the metal particles also plays a role. The metal particles with sharp corners can easily form a conductive path in non-circulating electrostatic spraying systems, thus when metal paint is electrostatically sprayed, a non-polar solvent and a circulation system should be used.
- Optimal conductivity range and adjustments : To achieve optimal charging and spraying results, the paint’s conductivity should be between 20M ohm to 30 M ohm. Changes can be made to make a coating more conductive, including solvent additions, changes in solvent composition, and the use of polar solvents. Viscosity corrections may also need to be made to ensure coating droplets are fine enough.